La impresión 3D está llamada a generar una revolución en nuestra sociedad actual y en la forma de diseñamos y fabricamos. El uso de esta tecnología aplicada a aleaciones metálicas avanzadas (fabricación aditiva metálica) permite un nuevo nivel de diseño y libertad geométrica. Es el caso de las estructuras reticulares complejas o “micro-andamios” que dotan al componente con un grado de optimización superior a los fabricados convencionalmente.
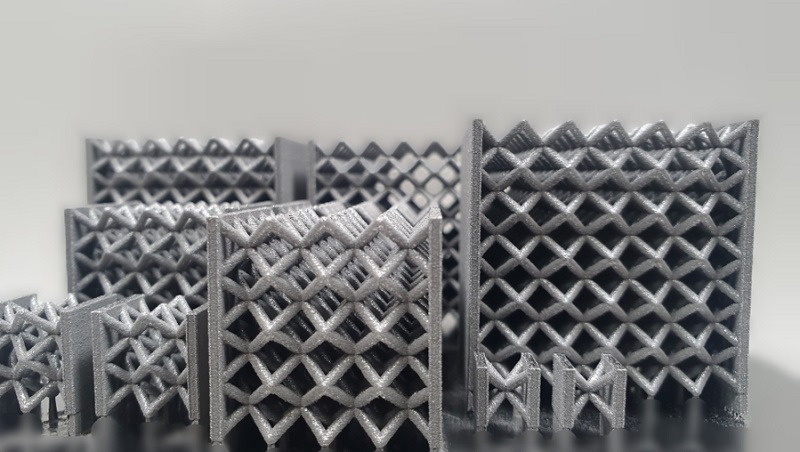
Esta ventaja esta llamada a revolucionar los sectores aeroespacial, energía, transporte o biomédico. El uso de estas estructuras de impresión 3D permitirá aviones más ligeros con alas reticulares o turbinas más verdes, coches y baterías más eficientes y seguros gracias a la integración de protección frente a impacto con sistemas de gestión de calor de la batería o implantes personalizados con una mayor osteointegración en el hueso del paciente.
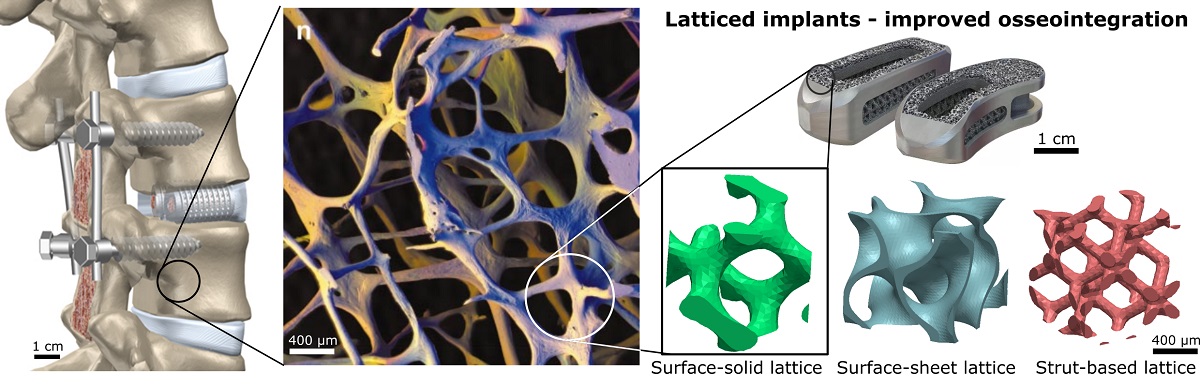
Sin embargo, estas estructuras metálicas fabricadas presentan problemas aún no resueltos en lo referido a la presencia de defectos y la predicción de sus propiedades mecánicas. Esto es de especial importancia para las aplicaciones citadas ya que sus componentes trabajan en muchos casos bajo condiciones extremas de cargas, temperatura o fatiga haciendo que su desarrollo quede frenado.
El grupo de investigación de la E.T.S. Ingeniería Aeronáutica y del Espacio “Materiales de Altas Prestaciones” (PERFORM -https://www.perform-upm.com) de la Universidad Politécnica de Madrid (UPM) ha dedicado sus esfuerzos en los últimos años en posibilitar la revolución digital de la fabricación aditiva y en solucionar muchos de los escollos que la impiden penetrar con éxito en los sectores aeroespacial, del transporte o biomédico. El grupo de Propiedades Mecánicas de Materiales bajo condiciones extremas de la E.T.S. de Ingenieros de Caminos, Canales y Puertos de la UPM centra sus esfuerzos en el entendimiento de las propiedades mecánicas de los materiales en condiciones de alta temperatura y/o impacto.
El proyecto ADDITXTREME financiado por la AEI busca desarrollar toda una nueva metodología que integre las peculiaridades del material metálico impreso en toda la etapa de fabricación y diseño del componente producido por impresión 3D. Esto se lleva a cabo frente el entendimiento científico de porque suceden los defectos durante la fabricación y como afectan estos al comportamiento mecánico de la aleación. Para ello se usarán dos aleaciones de uso aeroespacial: la aleación de titanio Ti6Al4V y la aleación de aluminio AlSi10Mg. Se fabricarán diferentes prototipos de micro-andamios y estructuras reticulares y se analizarán mediante microscopía electrónica avanzada y tomografía X-RAY la calidad del metal, su microestructura y la presencia de defectos.
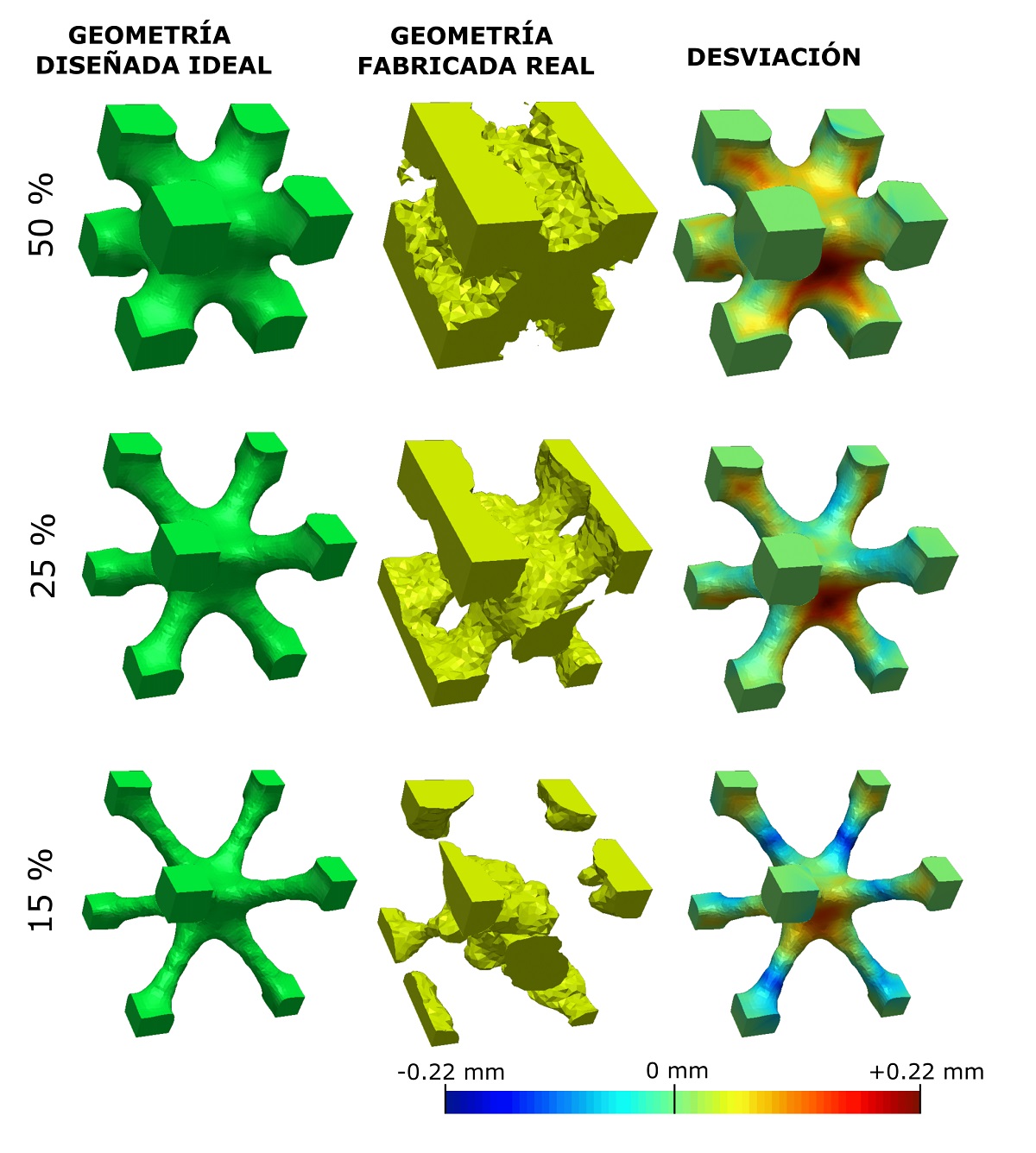
Tras esto se realizarán ensayos mecánicos de estos prototipos en las mismas condiciones extremas de carga y temperatura que presentarán en servicio para entender su comportamiento (Video). Por último, se incluirá ese nuevo entendimiento en herramientas de diseño y fabricación que mejoren la fiabilidad de estos componentes. ADDITXTREME es un proyecto fuertemente multidisciplinario que involucra a expertos de los campos de la fabricación, ciencia de materiales, modelado computacional o mecánica experimental en condiciones extremas. Este proyecto se espera que produzca conocimientos de vanguardia en el campo de materiales funcionales avanzados y fabricación aditiva.
Potencialmente, la metodología y entendimiento desarrollados ADDITXTREME aplicados a aleaciones avanzadas permitirá el desarrollo de nuevos materiales estructurados o “micro-andamios” más seguros y un proceso de diseño más fiable, lo que se espera que potencie el uso de estas estructuras en aplicaciones de gran demanda estructural como aviones, turbinas, satélites, automóviles o implantes óseos. El desarrollo de esta tecnología con base en España permitirá la ventaja competitiva de nuestras empresas lo que puede traducirse en nuevos puestos de trabajo atraídos por la industria aeroespacial, biomédica y de automoción nacionales o incluso nuevas empresas emergentes. Además del impacto económico, los avances de ADDITXTREME permitirán a la sociedad española tener a su disposición mejores implantes, vehículos eléctricos con mayor alcance y más seguros o un transporte aéreo más verde con un menor impacto ambiental.
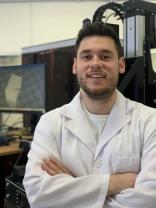
Daniel Barba Cancho es profesor del Departamento de Materiales Aeroespaciales de la Escuela Técnica Superior de Ingeniería Aeronáutica y Espacial de la Universidad Politécnica de Madrid (UPM). Se graduó en Ingeniería Aeroespacial en la UPM (2014) y posteriormente realizó su doctorado en la Universidad de Oxford (2018) desarrollando nuevas superaleaciones presentes en los motores a reacción de aviación. Su investigación actual se centra en combinar herramientas computacionales y experimentales para comprender el comportamiento mecánico de materiales de alto rendimiento usados en los campos aeroespacial y biomédico, específicamente aleaciones de titanio y superaleaciones base Ni. Actualmente está comenzando una nueva línea de investigación en Madrid centrada en la fabricación aditiva de aleaciones avanzadas y materiales funcionales para aplicaciones aeroespaciales y biomédicas.
PID2020-116440RA-I00